Die 5S-Methode ist eine partizipative Managementtechnik, die darauf abzielt, die Arbeitsumgebung eines Unternehmens zu verbessern, um sie zu einem sicheren und standardisierten Ort zu machen. Sie setzt voraus, dass die Mitarbeiter auf allen Ebenen der Organisation Verantwortung übernehmen. Denn eine Beteiligung auf allen Hierarchieebenen ist unerlässlich, um die Mitarbeiter dafür zu gewinnen und eine gemeinsame Unternehmenskultur zu schaffen. Hier sind die fünf Regeln, die durch diesen japanischen Verhaltenskodex aufgestellt wurden.
Was ist die 5S-Methode?
Die 5S-Methode stammt direkt aus Japan und ist ein Teil der Lean-Philosophie: Sie zielt darauf ab, den Arbeitsplatz besser zu organisieren, um die Effizienz zu steigern. Denn ein aufgeräumter und übersichtlich gestalteter Arbeitsplatz steigert nicht nur die Produktivität und die Qualität der Produktionsprozesse, sondern macht sie auch deutlich sicherer. Und da die Sicherheit gewährleistet ist, kann sich der Mitarbeiter besser auf seine wichtigen Aufgaben konzentrieren, also produktiv und leistungsfähig zu arbeiten.
Die 5 Schritte der 5S-Methode:
Seiri: Unnötiges aussortieren;
Seiso: (zum) Glänzen (bringen), säubern;
Seiton: den Arbeitsplatz optimal organisieren;
Seiketsu: die Regeln standardisieren;
Shitsuke: Selbstdisziplin üben.
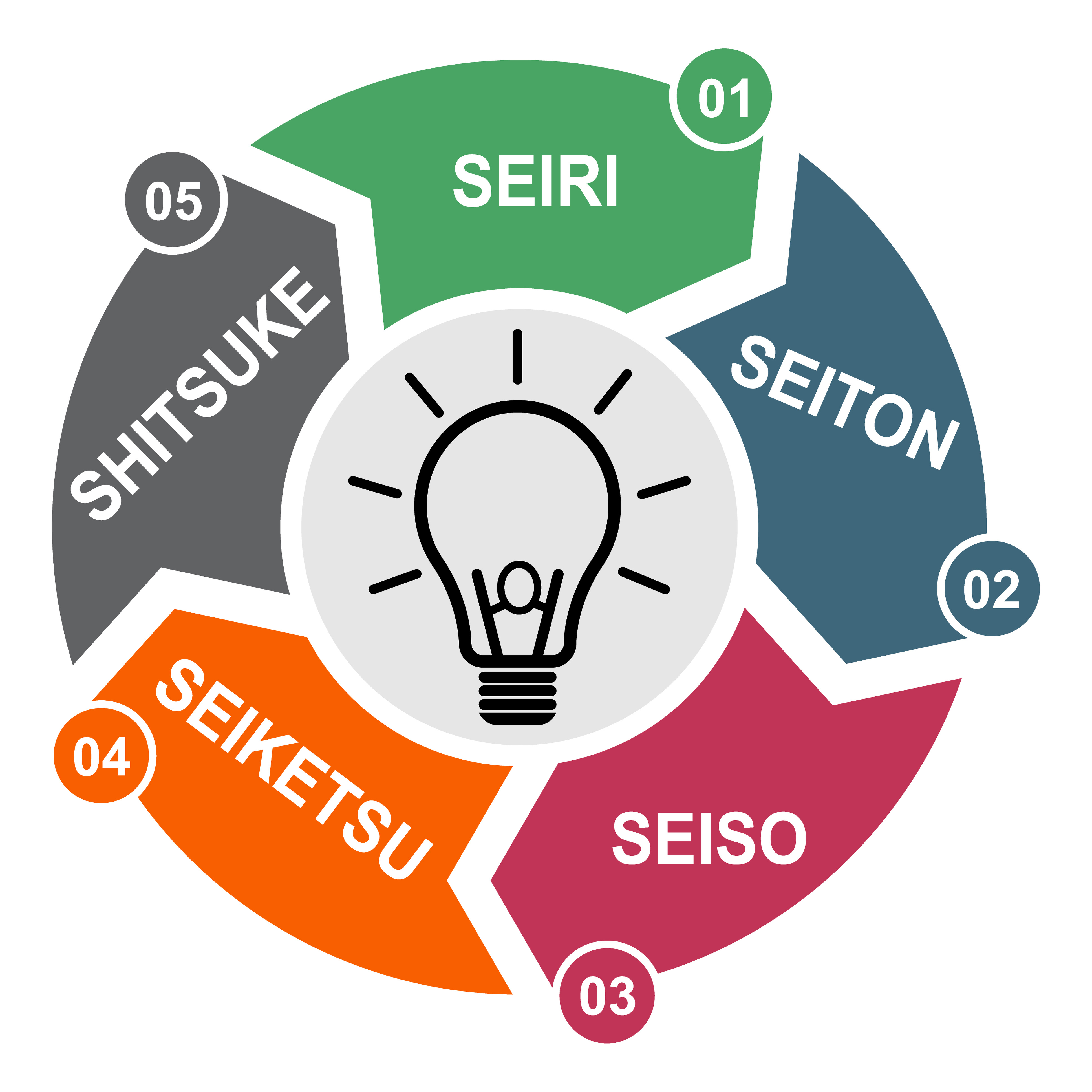
Nachfolgend werden die fünf Schritte im Einzelnen erläutert und was sie dem Unternehmen bringen.
Welche Vorteile bietet die 5S-Methode für das Unternehmen?
Diese Methode bietet zahlreiche Vorteile. Sie ermöglicht nämlich:
Die Unordnung zu reduzieren, den Verlust von Material oder Dokumenten zu verringern und so Verschwendung zu vermeiden;
Eine mögliche Beschädigung des Materials frühzeitig zu erkennen;
Verschiebungen in der Produktionskette und im Unternehmen insgesamt zu optimieren;
Die Effizienz der Teams auf allen Stufen der Produktion zu steigern;
Unfall- oder Gesundheitsrisiken zu vermeiden, insbesondere an Produktionsstätten, wo Risikomaterialien oder -werkzeuge zum Einsatz kommen;
Das Produktionstempo zu erhöhen, indem energieintensive Aufgaben mit geringer Wertschöpfung eliminiert werden;
Das Arbeitsumfeld angenehmer zu gestalten und so durch bessere Arbeitsbedingungen für ein größeres Engagement der Beschäftigten zu sorgen;
Die Endqualität der Produkte und den Output der Produktion zu verbessern.
Wie sieht die konkrete Anwendung der 5S-Methode aus?
Seiri, Seiton, Seiso, Seiketsu, Shitsuke – fünf japanische Begriffe, um diese Technik zur Optimierung des Arbeitsplatzes umzusetzen. Dies sind die wichtigsten Schritte, die Sie beachten sollten, um ein optimales Ergebnis zu erzielen.
Seiri
Seiri ist das japanische Wort für „aussortieren“. Hier geht es also darum, alles Unnötige aus dem Arbeitsbereich zu entfernen, um die Entstehung von Unordnung zu begrenzen und einen funktionaleren Raum zu schaffen. Die Phase Seiri umfasst folgende Maßnahmen:
Alles, was mindestens ein Jahr lang nicht benutzt wurde, wegwerfen oder recyceln;
Alles, was seit einem Monat nicht mehr benutzt wurde, aussortieren (Archiv oder Lagerraum im Werk);
Alle Gegenstände, die weniger als einmal pro Woche benutzt werden, in der Nähe des Arbeitsbereichs abstellen (z.B. Werkstattschrank oder Aufbewahrungsbox);
Alles, was weniger als einmal am Tag gebraucht wird, auf der Arbeitsfläche ablegen;
Alles, was weniger als einmal pro Stunde benutzt wird, auf der Arbeitsfläche und in unmittelbarer Reichweite ablegen;
Alles, was mindestens einmal pro Stunde gebraucht wird, direkt beim Mitarbeiter ablegen.
In der Phase Seiri geht es darum, im Einzelnen zu priorisieren, was weggeworfen und was aufbewahrt werden soll. Seiri ist besonders im Bereich von Fabriken und Werken anwendbar, wo viele Werkzeuge zum Einsatz kommen, wodurch die Produktion verlangsamt werden kann.
Der Anwendungsbereich von Seiri kann sich jedoch auch auf den Bürobereich erstrecken. Dann bezieht sich das Aussortieren auf zu schließende Fenster und Ordner des Computers, damit man sich nur auf das konzentriert, was in direktem Zusammenhang mit der zu erledigenden Aufgabe steht. Mithilfe von Seiri ist es so möglich, die Anzahl der Unterbrechungen zu reduzieren.
Seiton
Seiton ist das japanische Wort für „aufräumen“. Es geht darum, für alles (Werkzeuge, Akten, Vorräte) einen ganz bestimmten Platz festzulegen, damit es leicht und in kürzester Zeit auffindbar ist. Seiton könnte man mit dem Sprichwort zusammenfassen: „Ein Ort für alles, und alles an seinem Platz“. Die Phase Seiton muss bestimmten Regeln folgen:
Objekte entsprechend ihrer Nutzungshäufigkeit platzieren;
Die Platzierung der Objekte entsprechend ihrer Eigenschaften (Nähe, Gewicht, Platzbedarf) optimieren;
Ordnungsregeln nach festgelegten Kriterien (alphabetische Reihenfolge, Anwendungsbereich, Reihenfolge der Verwendung) aufstellen;
Die am häufigsten verwendeten Gegenstände in unmittelbarer Nähe ablegen;
Die Anordnung der Arbeitsplätze durch Standardisierung vereinfachen;
So oft wie möglich die FIFO-Methode (First In First Out) anwenden, um zu verhindern, dass sich Material oder Dokumente ansammeln. Wichtig ist eine nachvollziehbare Priorisierung.
Mit Seiton werden Zeitfresser verringert, die – obwohl sie nicht sehr groß sind – sich durch ihre Häufung als schädlich für die Produktivität erweisen können.
Seiso
Seiso bedeutet auf Deutsch „säubern“. Diese Phase zielt darauf ab, den Arbeitsbereich vollständig zu säubern, nachdem er zuvor freigeräumt (Seiri) und aufgeräumt (Seiton) wurde.
Neben der Sauberkeit ermöglicht Seiso, dem Auftreten von Fehlern bei Maschinen frühzeitig vorzubeugen, indem Probleme schnell erkannt werden oder die Ansammlung von Staub verhindert wird, was manchmal die Ursache für eine Werkzeugstörung sein kann.
Seiso ist also ein erster Schritt in Richtung einer eigenständigen Wartung, um frühzeitig einen vorzeitigen Verschleiß an Maschinen zu erkennen, der die Produktion für eine gewisse Zeit stilllegen könnte.
Ein sauberer Arbeitsplatz ist auch ein Sicherheitsfaktor, um Verletzungen, z.B. durch Ausrutschen oder austretende Flüssigkeiten, zu verhindern.
Ein sauberes Arbeitsumfeld trägt schließlich auch dazu bei, die Benutzerfreundlichkeit am Arbeitsplatz zu erhöhen. Seiso ermöglicht es also, in einem angenehmen Arbeitsumfeld und einer gesunden Umgebung zu arbeiten.
Seiketsu
In der Phase Seiketsu geht es darum, den Arbeitsplatz konsequent sauber, aufgeräumt und frei von allem Unnötigen zu halten. „Seiketsu“ könnte man also mit „die Ordnung aufrechterhalten“ übersetzen.
Dieser Begriff ist auch im Sinne von „standardisieren“ zu verstehen, also Regeln festzulegen, um den Arbeitsbereich in einem genau definierten Zustand zu halten. Es kann auch als eine Art visuelles Management gesehen werden, das darauf abzielt, alles, was dieser neuen Ordnung widersprechen könnte, zu identifizieren und sofort auszuschließen. Dies kann u.a. durch Farbcodes, das Intranet des Unternehmens oder eine Tafel mit Anweisungen (Whiteboard, Flipchart usw.) geschehen. Dieser Schritt der Standardisierung erfolgt durch die Einführung mehrerer Elemente, die auch die Grundlage für die letzte Phase der 5S bilden.
Klare Anweisungen erteilen
Auf der Hinweistafel sollten kurze und einfache Richtlinien vorgegeben werden. Mithilfe eines Schemas, einer Checkliste oder eines Flussdiagramms kann auf einfache Weise erläutert werden, was zu tun ist. Die Anweisungen müssen verständlich sein und können unterschiedliche Formen annehmen, z.B. das Foto eines Schranks, auf dem genau zu sehen ist, wo jeder Gegenstand aufbewahrt werden muss. Achten Sie auch darauf, dass die Anweisungen aus der Ferne lesbar sind.
Farbe ins Spiel bringen
Verwenden Sie so häufig wie möglich Farben. Mithilfe farbiger Aufkleber lassen sich beispielsweise die auszuführenden Arbeitsschritte besser visualisieren, z.B. „Für welche Produkte steht eine bestimmte Farbe?“ oder „Wer macht was?“.
Den richtigen Standort wählen
Hängen Sie die Hinweistafel an der richtigen Stelle auf, wo sie von möglichst vielen Personen gesehen wird, aber vor allem auch von den Betroffenen selbst.
Gefahren anzeigen
Darüber hinaus ist es wichtig, die Gefahren am Arbeitsplatz deutlich, auch visuell, zu kommunizieren. Denken Sie dabei z.B. an Explosions- und Strahlungsrisiken, Gefahren durch hohe Temperaturen und ätzende Stoffe usw. Die Verwendung spezieller Piktogramme an den richtigen Stellen, am besten in einem einheitlichen Stil und in Kombination mit einer farbigen Markierung, hilft Ihnen, Unfälle im Unternehmen zu vermeiden.
Shitsuke
Shitsuke bedeutet wörtlich übersetzt „respektieren“ und ist eine der Grundlagen der japanischen Kultur. Die Einhaltung der Regeln, die in den vorherigen 4 S aufgestellt wurden, ist das Leitmotiv von Shitsuke. Dieser Begriff kann auch mit „streng sein“ übersetzt werden.
Ziel ist es, das Ergebnis der Bemühungen langfristig zu erhalten. Dies geschieht vor allem durch eine interne Kommunikationspolitik bei allen Mitarbeitern durch das Auslegen von Zeichnungen, Schemata oder anderen Dokumenten an verschiedenen Stellen in den Räumlichkeiten. Ziel ist es, sie immer wieder an die zuvor erwähnten Prinzipien von Seiri, Seiso, Seiton und Seiketsu zu erinnern.
Diese von Shitsuke befürwortete Strenge darf jedoch bei den Mitarbeitern nicht zu rigoros umgesetzt werden, da sie sich sonst als kontraproduktiv erweisen könnte. Es ist von entscheidender Bedeutung, dass diese neuen Nutzungsmuster allmählich in ihrer Alltagsroutine Einzug halten. Trotz der Anwendung von Shitsuke sollte nicht sofort eine Politik der „Null Unordnung“ angestrebt werden.
Welche konkreten Ergebnisse bringt die Anwendung der 5S-Methode?
Die Anwendung der 5S-Methode führt zu konkreten Ergebnissen, die hauptsächlich auf zwei Ebenen beobachtet werden können.
Ergebnisse auf der Ebene der visuellen Auswirkungen
Die 5S ermöglichen:
Sofort sichtbare Sauberkeit im Arbeitsbereich, ein sehr positiver Aspekt vor allem bei Kundenbesuchen;
Eine klare, unterteilte visuelle Organisation;
Die Erhaltung des einwandfreien Betriebszustands von Materialien und Werkzeugen;
Die Verringerung des Risikos von Arbeitsunfällen und von Gesundheitsrisiken;
Die Beseitigung von Leerlaufzeiten und Verschwendung;
Die Verbesserung der Arbeitsbedingungen der Mitarbeiter.
Ergebnisse auf der Ebene des Verhaltens der Mitarbeiter
Die 5S stellen Folgendes dar:
Eine neue Herausforderung und ein Hinterfragen der Mitarbeiter, wodurch vermieden wird, dass sie sich auf ihren Erfolgen ausruhen;
Ein standardisiertes Verfahren, das von neuen Mitarbeitern leichter angewendet werden kann;
Eine Beteiligung der Mitarbeiter an einem gemeinsamen Gruppenprojekt (Unternehmenskultur) und damit ein besseres Engagement.